Mechanical ventilation is the process of providing artificial breathing support to a patient. More than half of critically ill patients require mechanical ventilation[1]. Though mechanical ventilation increases time for recuperation, it is known to have given rise to complications arising from over-distention of lungs leading to ventilator associated lung injury (VALI) and ventilator induced lung injury (VILI). This paper aims to develop a sensor to identify breathing efforts initiated by the patient and give back responses to the ventilator to regulate ventilation modes and tidal volumes delivered by the ventilator. This will significantly aid in reducing asynchrony between the patient efforts and the ventilator input, thus preventing lung injury. Towards this end, we have simulated and studied the effect of different kinds of dynamic loading and diaphragm membrane thickness of the sensor on its sensitivity on a basic design. Copyright © 2015 by ASME Country-Specific Mortality and Growth Failure in Infancy and Yound Children and Association With Material Stature Use interactive graphics and maps to view and sort country-specific infant and early dhildhood mortality and growth failure data and their association with maternal
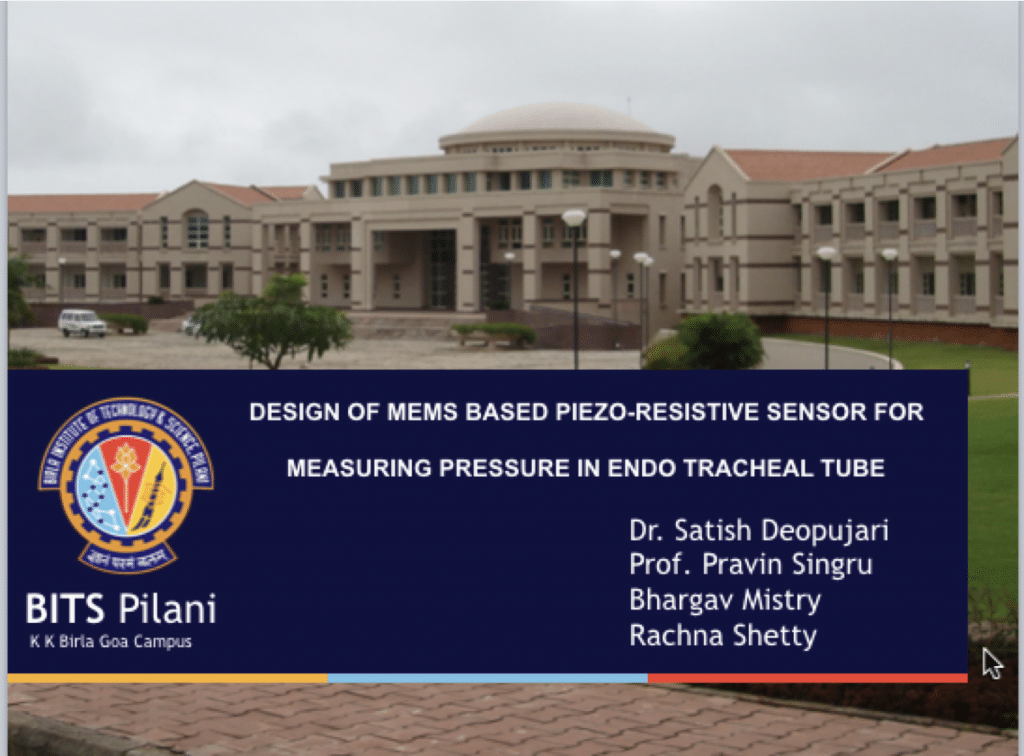
Piezoresistance is the phenomenon of change in electrical resistivity of a material on application of pressure or mechanical strain. This is largely observed in semiconductor materials such as silicon and germanium. The MEMS based piezoresistive pressure sensor exploits this property by measuring the change in resistivity through the amount of deflection produced in the diaphragm on the sensor and hence, the applied pressure.
The first usage of a MEMS sensor for biomedical applications dates back to 1967. Since then, MEMS devices have slowly progressed from pregnancy test kits to disposable blood pressure transducers, intra uterine pressure sensors, sensing in medical implants and body fluids, and various other healthcare support systems on account of its cost effectivity, small size, fast response time and high sensitivity. Most importantly, MEMS based sensors are less invasive. They have been widely used for blood pressure monitoring and measurement. In 1996, Omron released its first MEMS Capacitive-type Pressure Sensor, made on 4” MEMS wafers. They progressed to the
piezoresistive type of pressure sensor in September 2009, which led to reduced offset voltage, better energy savings. Mechanical ventilation is the process of assisted breathing to critically ill patients. But it has been observed that mechanical ventilation of disease-affected lungs, as well as being an inadequate mode of ventilation for initially healthy lungs, can cause significant changes in their structure and function. In order to differentiate these processes, two terms are used:
ventilator-associated lung injury (VALI) and ventilator-induced lung injury (VILI). In both cases, lung injury primarily results from differences in transpulmonary pressure – a consequence of an imbalance between lung stress and strain. To avoid this, synchrony must be achieved between patient efforts and ventilator efforts. This is where the role of a sensor comes into play.
This project aims to develop a MEMS based piezoresistive pressure sensor that measures inter tracheal pressure. This is to help in the regulation of air flow during mechanical ventilation. Although mechanical ventilation assists a patient in breathing, it can pose severe health risks, most common being ventilation associated pneumonia, ventilator-associated lung injury (VALI), and lung collapse. Many of these complications arise due to asynchrony in breathing efforts made by the patient and the ventilator response. High air pressure supply by the ventilator causes alveolar over-distension which ruptures the lungs by leading to lung collapse. Our sensor aims to solve this by sending back a response to the ventilator based on identification of the patient’s inspiratory efforts. This will indicate to the ventilator whether to start or stop inspiratory action or which mode of ventilation to use. Currently, this study is focused on getting accurate responses to simulated common dynamic loads from our preliminary design. Basic square, sawtooth and volume control waveforms were tested to check the sensitivity.
The sensitivity was also measured for various diaphragm thicknesses. It is observed that the sensitivity does not vary much with change in dynamic loading. Instead, it varies with diaphragm thickness.
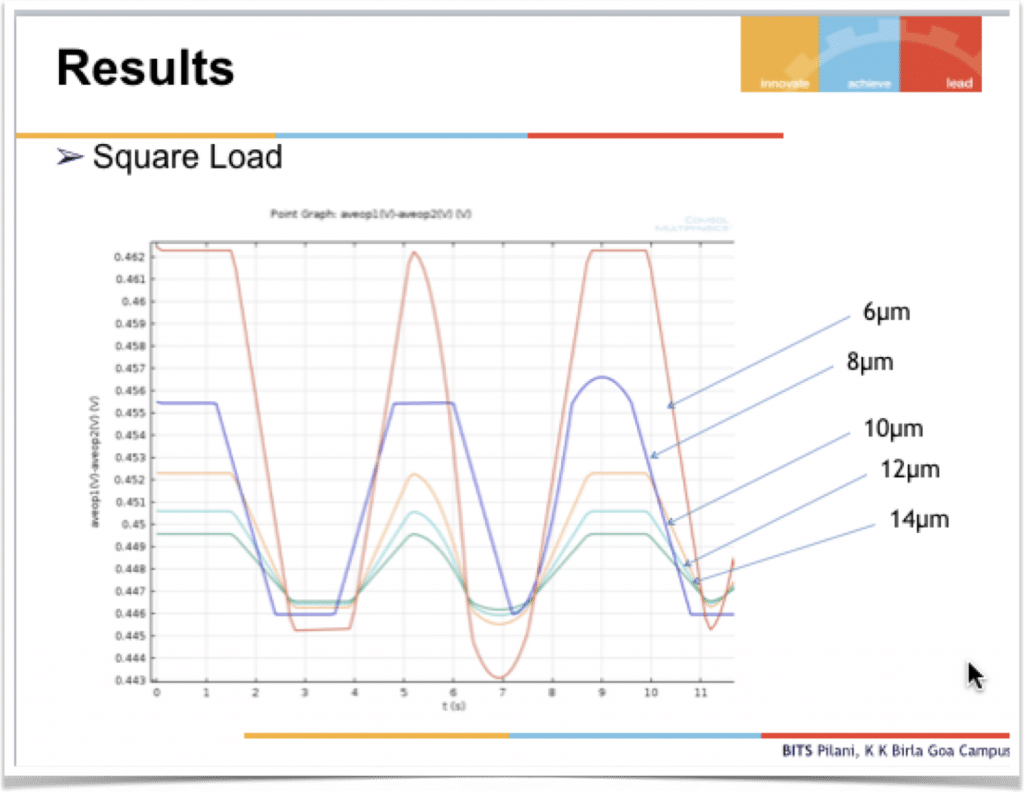
Conclusion
- An attempt was made to design a MEMS based sensor to accurately measure the intra tracheal pressure
- Three dynamic loads namely square load, sawtooth load and volume control loads were considered
- The design was analysed by varying the thickness of the membrane. It was observed that the amplitudes of the signal increased as the thickness of the membrane was reduced
- The sensitivity remained the same for different dynamic loads proving that it is independent of the applied load R